Basic Info.
Product Description
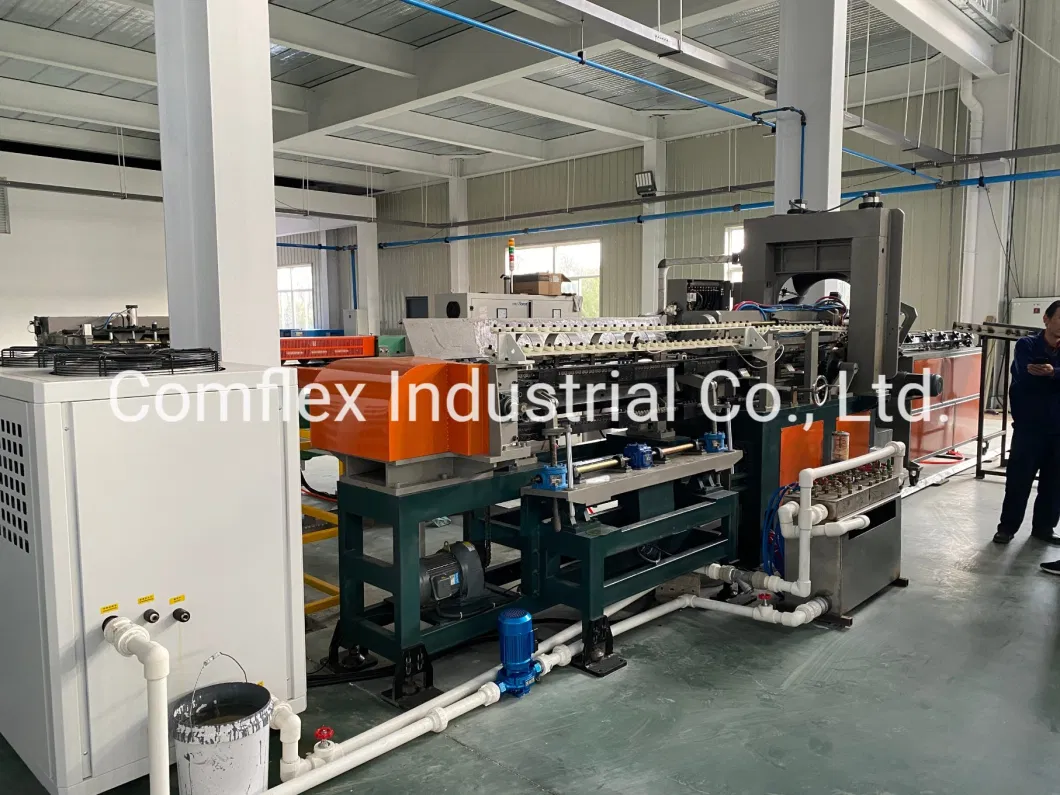
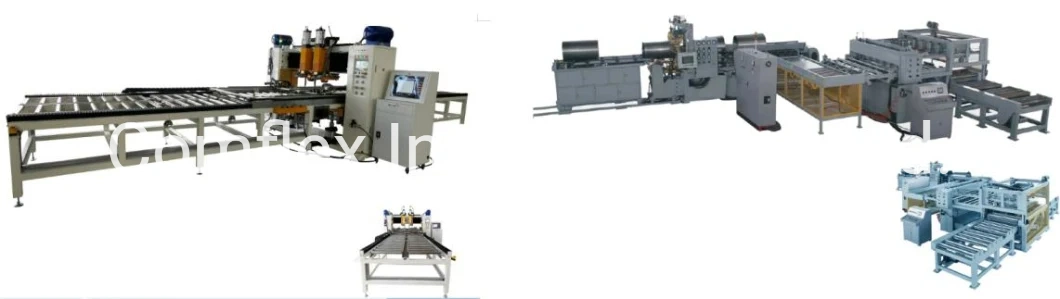
Inverter automatic steel drum seam welder (hereinafter referred to as seam welder) is an important device for producing metal drums. Its working principle belongs to the scope of resistance welding: that is, after the workpieces are assembled, the electrode applies pressure and the current flows through the steel plate. The contact area of the overlap and the adjacent area generate resistance heat, thereby forming a series of overlapped nuggets to obtain an airtight weld.
The welding method adopted by this equipment is roll seam welding. The electrode is a cylindrical roller. Its width is larger than the overlap of the steel plate to control the thickness of the joint. Welding uses a large electrode pressure and continuous welding current. By controlling welding specifications, including parameters such as electrode pressure, welding current, and welding speed, stable welding quality can be obtained, and seam welding procedures for longitudinal welds with a diameter of 560mm to 571.6mm can be completed.
The operation flow of this equipment: Manually put the cut sheet on the pedal, and automatically transfer it to the automatic slitter. After being automatically conveyed into the machine and rolled into a cylindrical shape, the spot welding is not necessary, that is, the steel drum is longitudinally welded. Seam welding, automatic unloading.
Main Technical Parameters
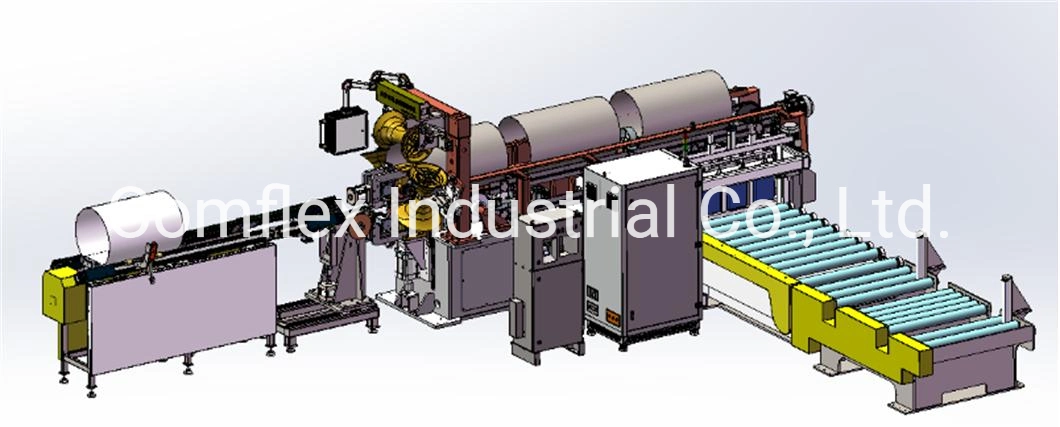
- Rated power:550KVA (Variable frequency, 250KVA at 100% duty cycle) 3 phase 380 V (10-400 Hz adjustable)
- Welding speed(Max):16m / min
- Productivity:12pcs/ min
- Welding drum inner diameter:φ560~φ571.5mm
- Welding drum length(drum height): <1000mm
- Welding Seam Overlap:2.5-3.5mm (High temperature and wear resistance, the thickness of the insert can be set)
- Steel plate thickness: 0.6-1.5mmmm(The tolerance of long and short sides is within ±0.5, the tolerance of the diagonal line within ±1)
- Compressed air pressure: 0.65 Mpa
- Cooling water:80 L/min 0.25Mpa(optional chiller)
Manually put the cut material on the pallet---Use the forklift (travel) on the feeding roller---automatic feeding by the suction cup---cut the edge (trimming) by the trimmer---to the rolling area- --Rolling---Drum walking---Welding area---Welding---Welding completed---Scissor tongue---Automatic unloading---Repeat the above actions
Other Types of seam welding machine:
Type I: Semi-automatic welding machine 2pcs/min
Main parameter description | Measure unit | Value |
Rated power | KVA | 200 |
Rated Input voltage | V | 380 |
Rated current | A | 526 |
Frequency | Hz | 50 |
Continuous Power | KVA | 140 |
Continuous Current | A | 370 |
Load Cycle | % | 50 |
Subprime no-load voltage | V | 6.8~7.6 |
Secondary voltage regulating series | 2 | |
Adjustable welding speed | m/min | 0.5~8 |
Rated welding thickness of weldment | mm | 1.5+1.5 |
Overlap Width | mm | 3.5~4 |
Extension elongation of electrode arm | mm | 1100 |
Adjustable top electrode strode | mm | 135 |
Maximum working pressure | N | 6000 |
Air pressure | MPa | 0.5 |
Cooling water consumption | L/h | 1300 |
Motor power | KW | 1.5 |
Weight of welder | kg | 2700 |
External dimension (length × width × height) | mm | 4400*1400*2200 |
Remark: Input voltage can be designed to suit the foreign country standard
Three-phase variable frequency controller Micro-computer controller
Type II: Spot welding machine+Longitudinal Seam Welding Machine
a: Spot welding machine
The spot welding machine is used to weld the metal by heating up the welding area-contact area of the welding work piece.Press and form a welding point. Type DN1-75 is used to spot welding, and it can be controlled precisely and form a good quality welds. The machine is completed with SUN08B control panel. The wall thickness for mild steel is 2.5+2.5mm.
Description | Unit | Parameters |
Rated capacity | KVA | 75 |
Rated voltage | V | 400 |
Rated current | A | 263 |
Frequency | HZ | 60 |
Continuous capacity | KVA | 45 |
Continuous Current | A | 118 |
utilization factor | % | 20 |
Secondary non-load voltage | V | 3.65-7.3 |
Secondary voltage adjust steps | 8 | |
Secondary voltage rated steps | 7 | |
Max.welding thickness | mm | 3+3 |
Rated welding thickness | mm | 2+2 |
Electrode arm length | mm | 800 |
Upper electrode adjustable stroke | mm | 20 |
Max.working pressure | mm | 11500 |
Air pressure | mm | 0.5 |
Cooling water consumption | kg | 700 |
Weight of the machine | kg | 850 |
Outer dimensions | mm | 1610*730*1460 |
b: Longitudinal Seam Welding Machine
The seam welder is widely used to weld the steel strips into cylinder. When welding, the two working pieces are overlapped between two welding wheels and pressed together. Connect the power, the welding wheels turn. When the welding wheels turn onto the overlapped area, the high temperature between two wheels makes nugget on the cylinder. The welding current is generated by impulsing power source. The seam welder is used to weld simple thin wall carbon steel cylinder without coating and mid-steel and alloy steel plate.
Description | Unit | Data | |
Rated Capacity | KVA | 200 | |
Primary voltage | V | 400 | |
Frequency | HZ | 60 | |
Rated load succession rate | % | 60 | |
Secondary non-load voltage | V | 6.8-7.6 | |
Secondary voltage adjust steps | 2 | ||
Rated steps | 2 | ||
Max. thickness of the work piece | MM | 2+2 | |
Rated welding thickness | MM | 1.5+1.5 | |
Electrode arm length | MM | 1100 | |
Effective length for different ID cylinder | ID 360mm | MM | 480 |
ID 440mm | MM | 730 | |
ID 600mm | MM | 1100 | |
Upper welding wheel initial stroke | MM | 55 | |
Max stroke | MM | 130 | |
Welding speed | M/MIN | 1-8 | |
Max. working pressure | N | 6000 | |
Air source compressed air pressure | MPa | 0.5 | |
Air consumption (natural status) | M3/H | 2.5 | |
Cooling water consumption | L/H | 1300 | |
Weight | KG | 3000 |
Customer Visiting
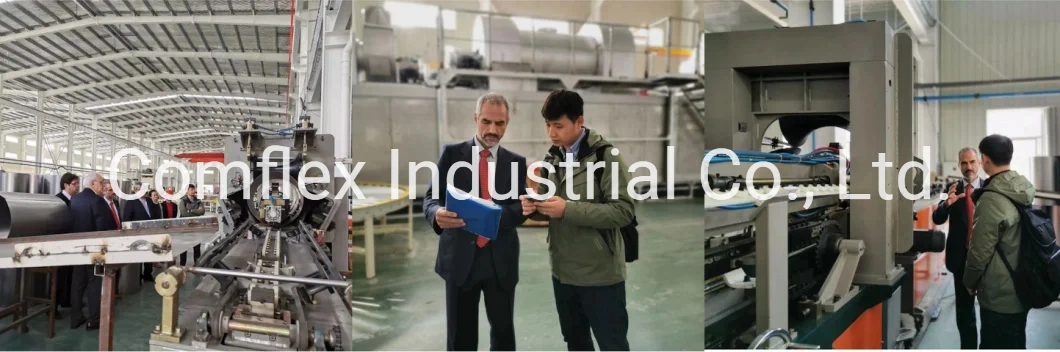
Packaging &Shipping
Packaging Details: Standard seaworthy packing
Delivery Time: 3 months after receving your advance payment
FAQ
To enable me give you correct proposal for correct machines, please tell me following details:
A: Technical drawing/Size of the steel drum you want to manufacture
B: What's the capacity per shift/day?